- News
15 May 2014
EVG wafer bonding and bond alignment systems installed at Penn
EV Group (EVG) of St Florian, Austria (a supplier of wafer bonding and lithography equipment for MEMS, nanotechnology and semiconductor applications) has shipped an EVG510 semi-automated wafer bonding system and an EVG620 automated bond alignment system to the University of Pennsylvania (Penn). The systems are installed in the Quattrone Nanofabrication Facility in the Singh Center for Nanotechnology at Penn in Philadelphia, where they are being used for anodic and thermocompression bonding processes in the fabrication of advanced micro- and nano-systems.
“Academic institutions like the University of Pennsylvania provide critical contributions to advanced research and development across a multitude of high-technology industries,” comments EVG’s chief scientist Dr Viorel Dragoi. “Penn’s Quattrone Nanofabrication Facility is using our wafer bonder and bonding alignment systems to help their students, faculty and corporate partners to move their cutting-edge research forward into new and exciting nanotechnology applications.”
The Quattrone Nanofabrication Facility is a multi-user facility serving the nanofabrication needs of the Penn community as well as those of external users. It houses a suite of tools for micro- and nano-fabrication, including optical and electron-beam lithography, vapor deposition, etching, packaging and electrical testing. Adding bonding capabilities via the EVG510 and EVG620 systems enables the facility to implement new processes that can support applications such as microfluidics, MEMS, and heterogeneous integration.
The EVG510 wafer bonding system provides fully automated processing with manual loading and unloading. It features EV Group’s field-proven uniform heating and pressure application systems. With a modular bond chamber design that accommodates wafer sizes up to 200mm, the EVG510 is claimed to provide the lowest cost-of-ownership for both R&D and pilot-line production. The EVG620 system supports bond alignment of double- or triple-wafer stacks up to 150mm wafer sizes, and offers what is claimed to be the highest precision, flexibility, ease of use and modular upgrade capability.
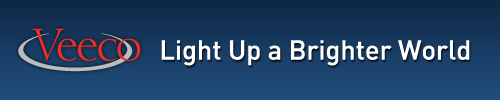