- News
28 October 2013
Osram's new wafer fabrication building in Penang certified as a Green Building
Osram Opto Semiconductors GmbH of Regensburg, Germany says that its new Pen32 wafer fabrication plant in Penang, Malaysia, has been certified as a Green Building, conforming to requirements on design and construction under the Green Building Index (GBI). The new building aligns with Osram’s standards for fabrication sites and is said to be one of the first industrial buildings in Malaysia to have been awarded the certification, following close scrutiny on design and construction.
Picture: Pen32, Osram Opto’s new wafer production building, has been certified as ‘green’ from design to construction.
GBI looks at the efficient use of resources (such as energy, water, and materials) and the reduction of building impact on human health and environment during a building’s lifecycle. It is challenging for an industrial building to meet these criteria, notes Osram Opto.
“Right from the beginning when we planned to build a new wafer facility here, we wanted it to have minimal impact on its surroundings,” says Dr Roland Mueller, managing director of Osram Opto Semiconductors (M) Sdn Bhd. “Not only can we achieve savings in our operations, but also we can show that we are committed for a better future for the people and environment around us.”
Starting with the construction phase, amenities have been made available and accessible to the project workers. Care was taken not to be the source of pollution during and after construction, says the firm. All construction materials are acquired locally (in line with GBI requirement), while refrigerants and cleaning agents are of non-ozone-depleting types. Waste is removed properly on a daily basis and stations are set up to collect materials that can be recycled.
Penang has an equatorial climate. So, to cool the building and to lower the overall building thermal transfer value to within GBI-acceptable levels, several measures are taken. The use of thermal-efficient bricks and low-emissivity glass, together with adequate insulation, significantly reduces the overall thermal transfer. Energy usage is optimized through the use of lighting zoning, relevant energy monitoring sub-meters, and medium-temperature chillers. Pumping systems are fitted with variable-speed drives to cater for different usage, further reducing energy needs.
Indoor environment quality also forms part of the GBI. To keep indoor air quality fresh, air handling systems are installed with CO2 monitoring sensors to modulate fresh-air intakes. Also, to reduce smells and fumes, low-VOC (volatile organic compounds) paints, adhesives and carpets are used. Adequate external views are made accessible from anywhere within the building to mitigate claustrophobic feelings and to create a more relaxed environment. Architectural and mechanical design efforts are made to provide comfortable lighting as well as to lower glare effect and noise levels for people working in the building.
In operation, most of the plant’s process waste water is reused as cooling tower recycling water. Water-efficient fittings are used to minimize water wastage in wash rooms. Heat pumps and a chilled water degassing system are innovative features adopted to achieve the GBI certification, says the firm.
“Pen32 is to last for years and, according to the GBI rating scheme, it has to be re-assessed every three years in order to maintain its status as a Green Building,” notes Mueller. “We will make every effort to ensure that the building will continue to have minimal impact on its surroundings and to provide a quality working place for our employees throughout its lifecycle.”
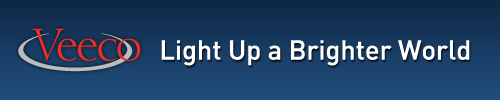